The main known variants of technological processes for manufacturing threads on a thread-rolling tool are described. Recommendations are given on the prospect of their application for various cases. A number of specific requirements are imposed on threaded profiles made on thread-rolling tools (rollers, segments, flat dies, chipless taps), which differ somewhat from the requirements for conventional running and, especially, mounting threads. In addition to high accuracy and low roughness, they must have high hardness and increased fatigue strength.
Since the main work on metal deformation during threading is performed by the tops of the tool thread turns, they should not have defects that are allowed for other types of threads. In this regard, the development of a rational technological process for manufacturing threads on a thread-rolling tool, which allows ensuring the fulfillment of all the above requirements, is a very difficult task.
Телефон для связи : WhatsApp
Currently, the most widespread are 3 methods of forming threads on a thread-rolling tool: rolling with a master screw, cutting with a blade tool (cutter or milling cutter) and thread grinding.
Thread grinding allows you to obtain threads of the highest accuracy. However, thread grinding is characterized by extremely low productivity. In addition, thread-grinding equipment is very expensive and demanding to the operating conditions. In this regard, the cost of a thread-grinding operation can be up to 50% of the total cost of a thread-rolling tool. The use of thread grinding can lead to a significant decrease in the resistance of the thread-rolling tool due to the deterioration of the structure of the surface layer due to caricature and cauterization.
It is possible to minimize the negative impact of thread grinding on the durability of the thread-rolling tool by using grinding wheels made of cubic boron nitride [2], circles with intermittent contact and highly porous circles [5], using coolant with surfactants. However, these measures are quite expensive and cost-effective only in the conditions of mass production of thread-rolling tools, which is why they are currently carried out only at specialized tool factories and in the tool industries of large industrial enterprises. In addition, it is currently not possible to completely eliminate (for example, by using low tempering) such defects in the surface layer of the thread turns after grinding, such as, for example, an unfavorable distribution of residual stresses.
You can find out about all the nuances of the order by calling the contact phone number listed on the company’s website.
Call us by phone:
+7 (495) 223-64-73
+7 (495) 726-11-08
and you will not regret it.
Rolling is the most high-performance method of thread forming. However, it can be carried out only on workpieces of relatively low hardness and in the manufacture of thread-rolling tools can be made only before its thermal hardening. In this regard, as a finishing thread-forming operation, it can only be used in the manufacture of a tool for rolling threads of low accuracy. In addition, when rolling, folds often occur at the tops of the thread (sunsets), which does not affect the quality of the running and mounting threads, but is important for the thread-rolling tool.
Traditional technological methods [4, 6] for eliminating sunsets, which consist in cutting off the defective thread vertices on the workpiece with subsequent rolling up to the full height of the profile, do not provide stable elimination of this defect, especially for large-pitch threads (more than 3 mm). In addition, carrying out several additional thread adjustments on thread-rolling tools made of low-plastic die steels sometimes leads to the exhaustion of the reserve of plasticity of the material and the appearance of cracks on the sides of the profile. The problem of eliminating sunsets requires a large amount of theoretical and experimental research to improve the deformation scheme during thread rolling.
At the same time, if there are no defects in the form of cracks and sunsets on the knurled threaded profile of the thread-rolling tool, its durability can be several times higher than the durability of the thread-rolling tool with a polished thread profile. The reason for this is that when rolling, such positive changes occur in the structure of the metal (for example, the grinding of carbide inclusions and a decrease in the score of carbide inhomogeneity), which persist even after heat treatment.
Threading with a blade tool (for thread – rolling rollers-a cutter, for flat dies – thread milling) is currently performed, as a rule, before the thermal hardening of the workpiece [1]. Such a technology has no prospects due to the low quality of the resulting profile. More promising is threading on a workpiece thermally hardened to a hardness of 58 … 63 HRC with a blade tool with a cutting part made of superhard materials (composites based on cubic boron nitride, mineral ceramics). Blade processing, unlike thread grinding, practically does not cause negative changes in the surface layer, and, thereby, contributes to increasing the durability of the thread-rolling tool. When using modern precision CNC machines as thread-forming equipment, the accuracy and roughness of the cut thread approaches the ground one. A significant advantage of threading with a blade tool is its high flexibility, which allows processing threads of various sizes with one tool, which makes it preferable for single production.
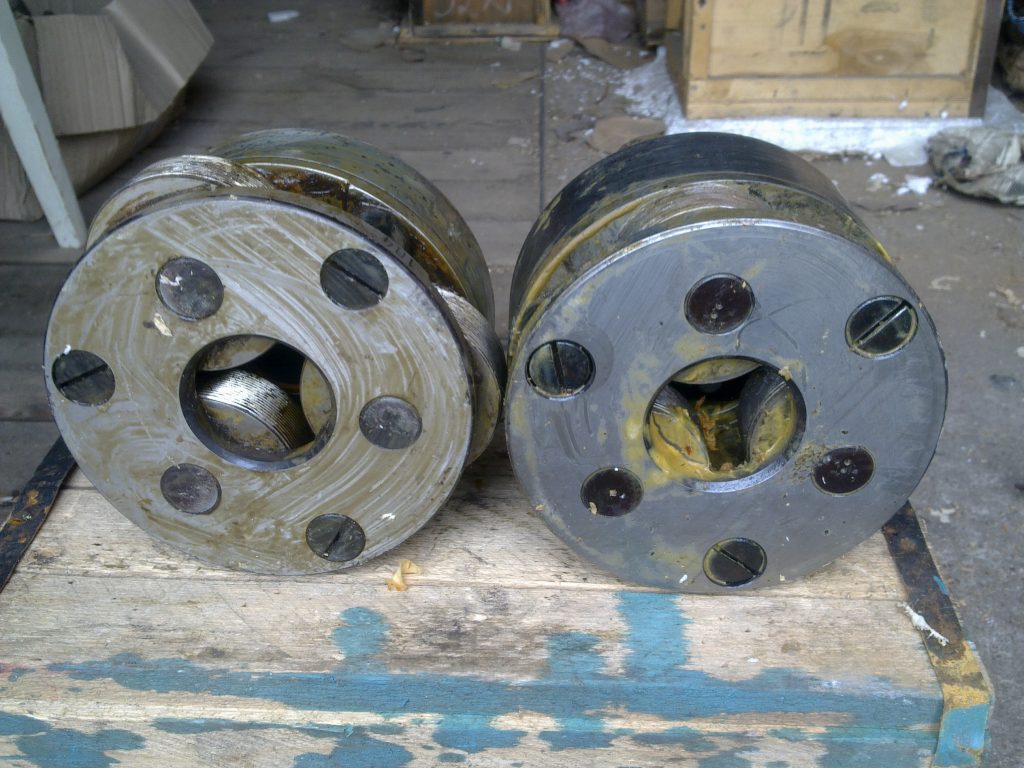
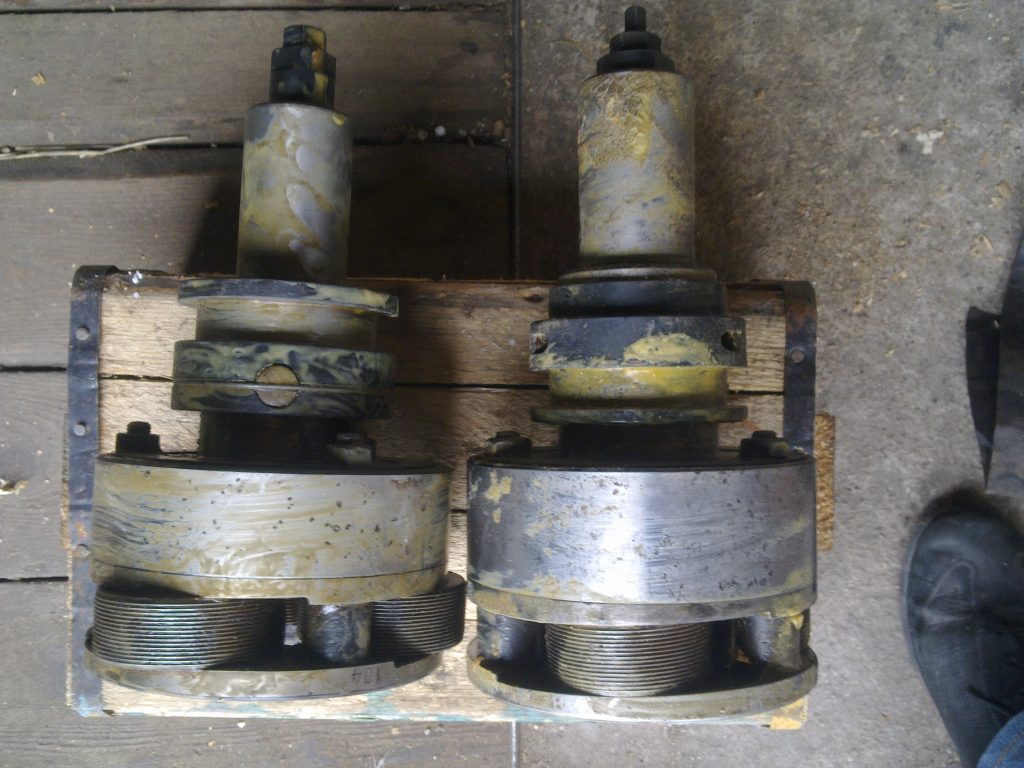
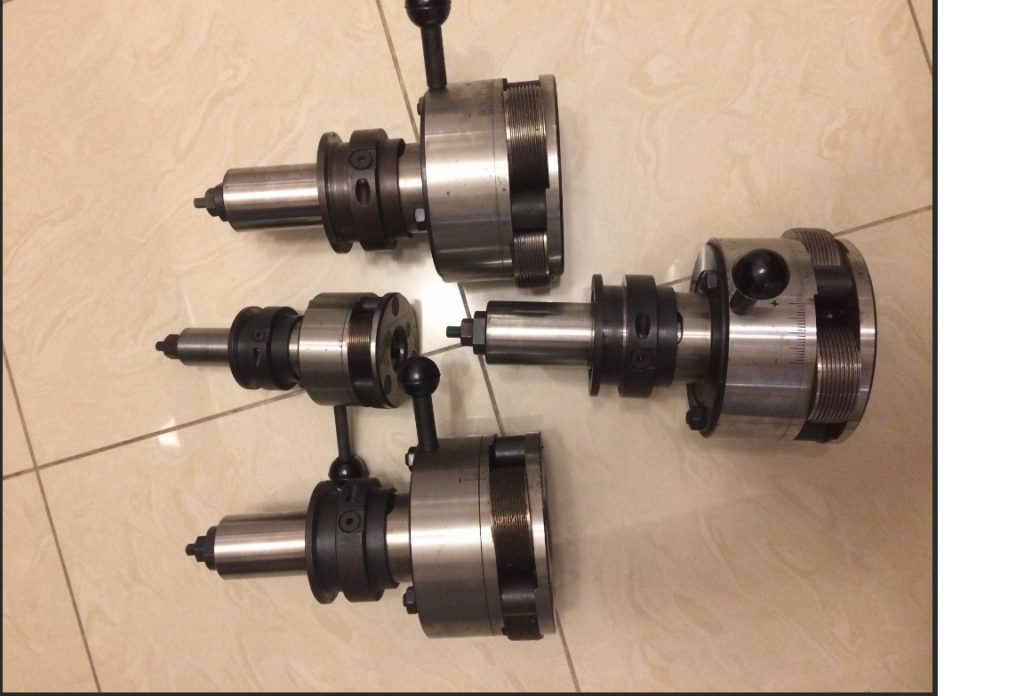
The most promising from the point of view of ensuring the required quality and increasing the durability of a thread-rolling tool is a combined technology for forming threads on it, which includes pre-rolling the thread on an uncoated workpiece, followed by the final formation of the thread after heat treatment using blade processing with a tool made of superhard materials or thread grinding (with particularly high requirements for accuracy and roughness of the threaded profile). The use of such a technology will not lead to a significant increase in the cost of threading tools, and in some cases will even reduce it due to the high productivity of threading and a significant reduction in the time for blade processing or thread grinding when processing threads along a pre-formed screw groove. The durability of a thread-rolling tool made using a combined technology corresponds to the durability of a tool with a knurled profile that does not have defects, and is stable, since defects that often occur during rolling are completely removed during subsequent processing.
Thread rolling head for CNC machine lathe milling machine high precision thread rolling systems
1 – 4 Sets
$1,500.00
$1,470.00
In order to increase the durability of the tool for rolling threads with a large step, it is advisable to increase the depth of deformation hardening of its threaded profile. This can be achieved by using, instead of the usual rolling, static-pulse processing (SIO) [3], carried out under conditions of a combination of periodic dynamic and constant static effects of the deforming tool on the surface to be processed. The depth of hardening with SIO can reach 10 mm or more, which is significantly higher than with traditional threading.
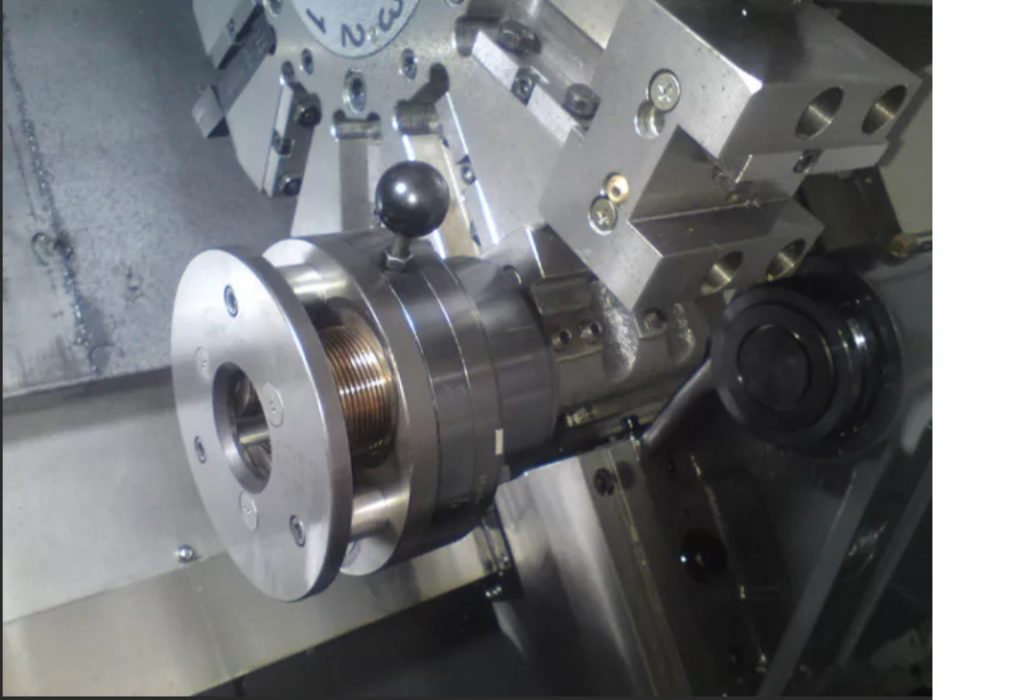
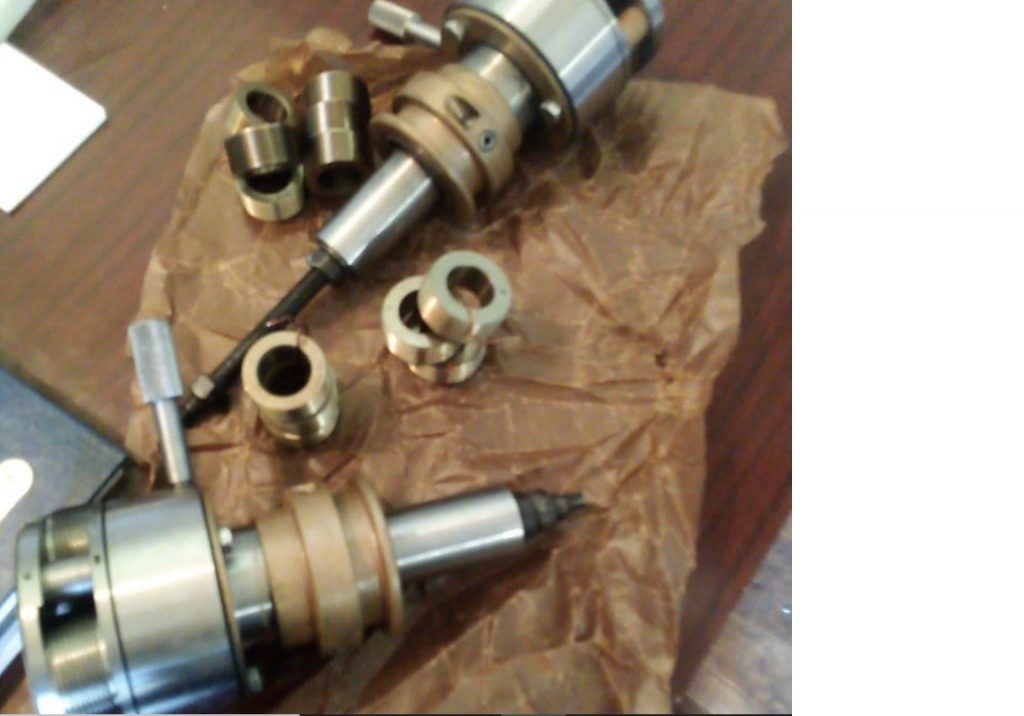
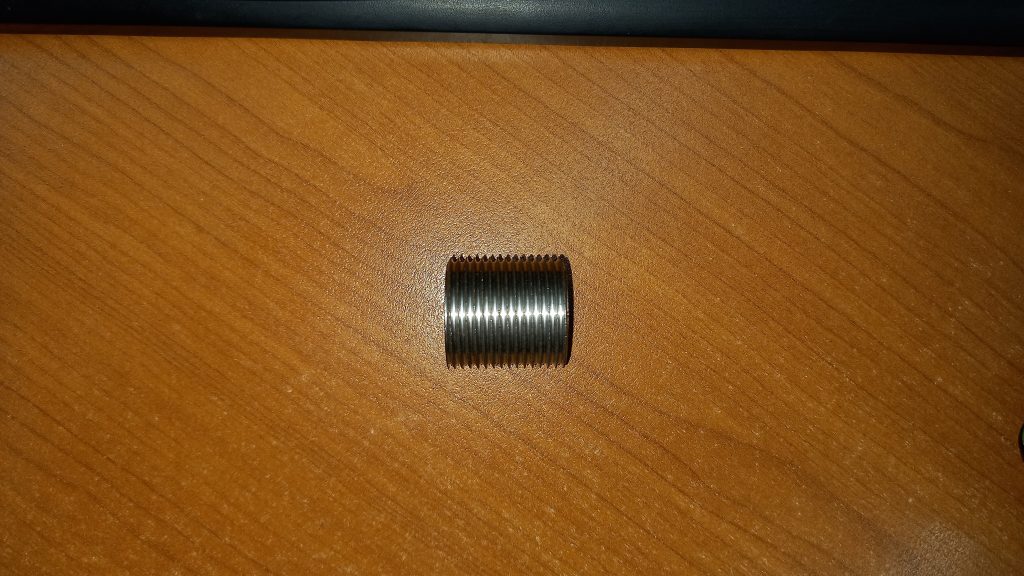
After forming the thread by blade processing or thread grinding to remove the tensile residual stresses and, consequently, increase the fatigue resistance of the thread-rolling tool, it is advisable to carry out a hardening treatment by surface plastic deformation-shot blasting, abrasive jet [7], smoothing, needle cutters, etc. At the same time, the characteristics of the hardening tool and the processing modes should be selected in such a way as to exclude a decrease in accuracy or a deterioration in the roughness of the thread turns.
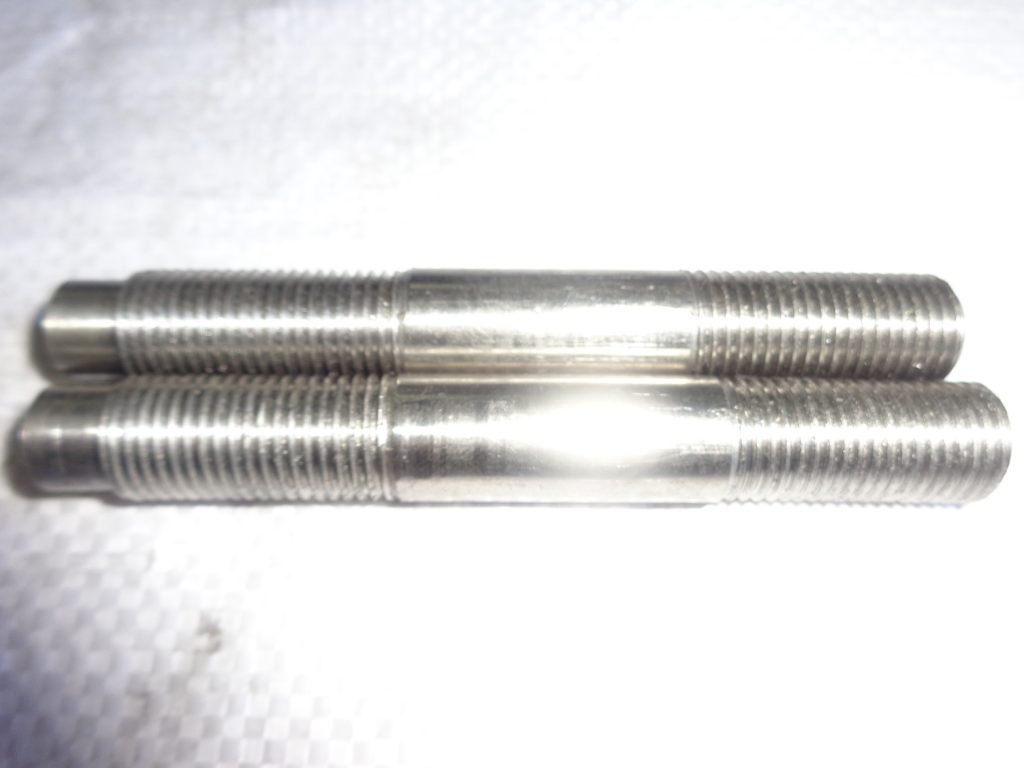
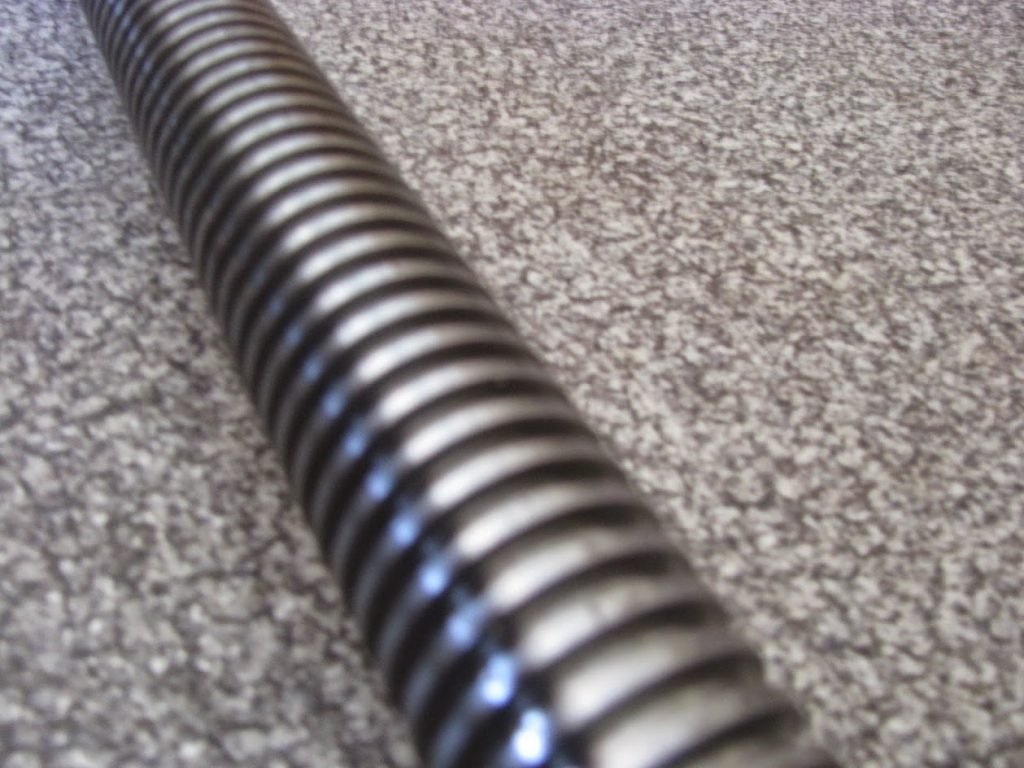
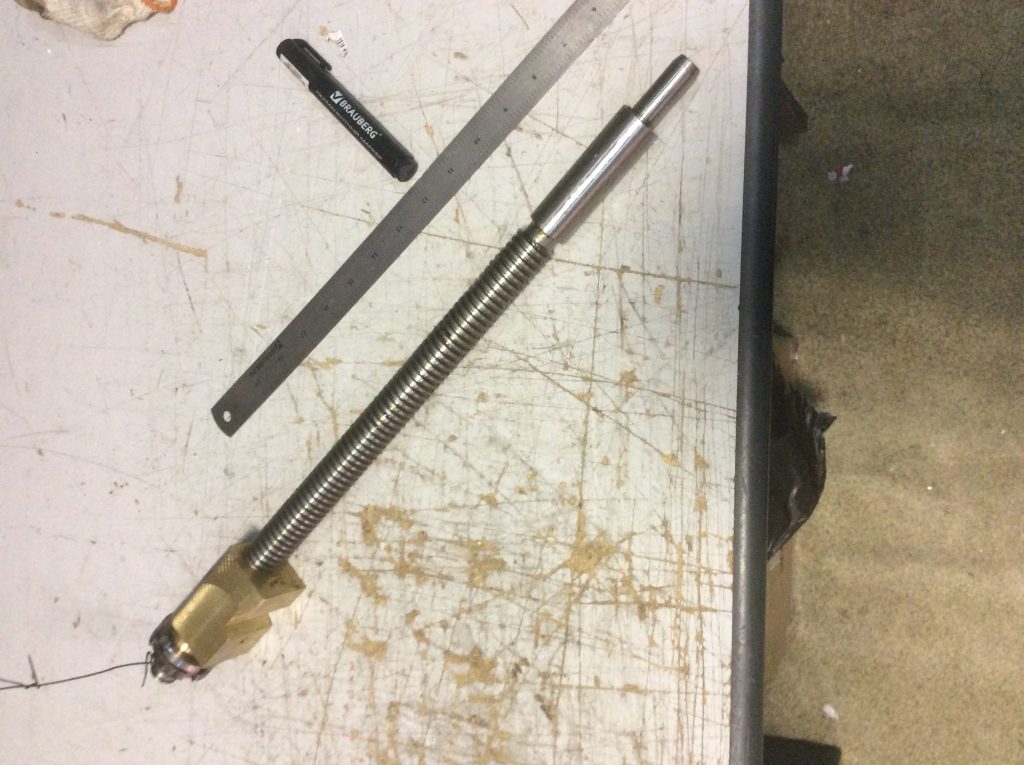
The most significant factor constraining the practical application of such a promising combined technology of thread forming is that its technological parameters (modes, distribution of allowance between thread-forming operations, etc.) are currently poorly studied and the technology has not yet been sufficiently developed. Conducting research in this area is one of the main directions of improving the thread-rolling tool.
Literature
Bobrov V. F. Multi-pass cutting of fastening threads with a cutter. Moscow: Mashinostroenie, 1982. – 104 p.
Zakharenko I. P., Akhunova I. M., Beletsky E. A. Tool thread grinding with circles made of kubonite. Moscow: Mashinostroenie, 1974. -144 p.
Kirichek A.V., Afonin A. N., Zaitsev A. N. Static-pulse processing of threads and profiles // Izvestiya of Tula State University, 2000, Issue 6. – pp. 81-96.
Menshakov V. M., Urlapov G. P., Sereda V. S. Chipless taps. Moscow: Mashinostroenie, 1976. – 167 p.
Polkanov E. G. Thread grinding with highly porous abrasive wheels. // Technology of Mechanical Engineering, 2002, No. 6. – pp. 17-19.
Selchukov A.D. Technology of manufacturing flat dies and thread-rolling rollers with sectors in the conditions of the Krasnaya Etna plant / / Thread-forming tool. Proceedings of the conference. Moscow: NIIMASH Printing House, 1968. – pp. 167-173.
Yakukhin V. G., Stavrov V. A. Production of threads. Reference book. Moscow: Mashinostroenie, 1989. – 192 p.